Kupol utiliza la impresión 3D para reinventar la forma en que se diseñan los cascos de bicicleta
Kupol utiliza la impresión 3D para reinventar la forma en que se diseñan los cascos de bicicleta
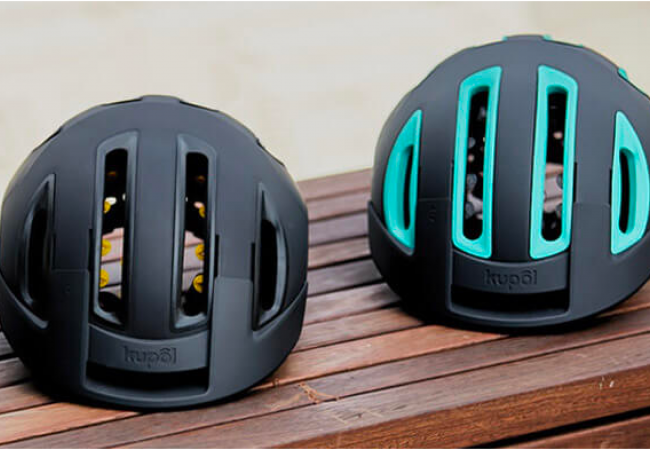
Bienes de Consumo
Cascos deportivos
HP 3D de alta reutilización PA 12 con micro esferas de vidrio
Bienes de Consumo
Cascos deportivos
HP 3D de alta reutilización PA 12 con micro esferas de vidrio
Bienes de Consumo
Cascos deportivos
HP 3D de alta reutilización PA 12 con micro esferas de vidrio
Kupol es una empresa innovadora fundada en 2016 por Gabriel Boutin, un diseñador que ha estado trabajando en cascos durante varios años antes de este proyecto. Fascinado por el potencial de la fabricación aditiva, Gabriel Boutin decidió utilizar la tecnología de impresión 3D Multi Jet Fusion para su proceso de desarrollo de productos.
"He estado diseñando cascos para bicicletas durante más de siete años", dice el director del proyecto Kupol, Gabriel Boutin. “Hubo muchas limitaciones con la fabricación en masa y especialmente cuando se usa espuma de poliestireno expandido (EPS) tradicional para el interior del casco. Mi papel como diseñador es repensar los productos para mejorarlos. Quería crear un casco que fuera más liviano y funcional ", dice el director del proyecto Kupol, Gabriel Boutin.
Los cascos de bicicleta se fabrican tradicionalmente en dos piezas. El exterior está hecho de plástico moldeado por inyección. El interior está hecho de espuma EPS y luego los dos se combinan para formar el producto final.
Debido a que se basan en métodos de fabricación en masa, el primer gran desafío es que ambas tecnologías requieren un compromiso de altos volúmenes. Además de crear un costo inicial significativo, esto también limita las oportunidades de personalización. Además, la espuma EPS repele la humedad y atrapa el calor en la cabeza del ciclista. Si bien los cascos modernos incluyen ranuras de enfriamiento para ayudar a mitigar este problema, no lo eliminan por completo.
El Sr. Boutin comenzó creando un nuevo diseño de casco que eliminaría la necesidad de espuma EPS. Creó una estructura abierta dentro de la carcasa del casco que permitiría la personalización y al mismo tiempo mejoraría la transpirabilidad.
Antes de trabajar con la tecnología de HP, el Sr. Boutin había probado otros métodos de impresión 3D, incluidos FDM, SLA y SLS, pero eran muy lentos y ninguno podía proporcionar la fuerza anisotrópica que necesitaba, especialmente teniendo en cuenta las paredes delgadas que necesitaba usar en su diseño. Además, el acabado de la superficie y la menor porosidad de Multi Jet Fusion le permitieron crear un diseño comercialmente atractivo.
Kupol pudo producir un producto que funcionó exactamente como lo había concebido el Sr. Boutin. El peso del casco se redujo en un 20%, fue tres veces más rápido de producir que con SLS, y la consistencia de la producción aseguró que cada casco funcionaría según lo previsto. El costo por pieza también estuvo en línea con las expectativas, lo cual fue importante porque el sistema de absorción de impactos de Kupol solo se puede fabricar utilizando una tecnología aditiva.
Con las pruebas completas, el Proyecto Kupol finalmente tenía un producto que estaba listo para salir al mercado.